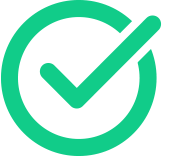
Use Kanban to manage demand driven inventory
In online retail inventory management, Kanban can be used to align inventory with actual customer needs. The store owner can use the Kanban to trigger replenishment, depending on the threshold. You can make inventory close to actual demand.
The Kanban system is inspired by retail stores, or more precisely, supermarket clerks, who replenish goods every time they sell them to customers.
Solve the problem of insufficient goods and low efficiency. Control the inventory in the best way
Using the "just in time" (JIT) method, strictly control orders, and drive a certain combination of algorithms based on long-standing intuition and predictive data.
Using Kanban in retail stores, suppliers do not directly replenish inventory based on their own estimates, but when a product is almost sold out, shop assistants can order new products. Therefore, the replenishment of inventory is completely demand-driven.
The Kanban card is a key component of the Kanban system. In short: In lean production, a Kanban card shows that a certain product has been sold and starts a new task in the production process. Inventory needs to be restocked and new products need to be produced.
The Kanban card visualization supports the entire production process. In this way, the Kanban system encourages demand-oriented systems, on-time production and continuous improvement, especially in avoiding waste.