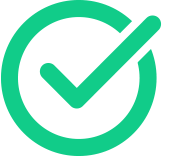
Use Kanban to eliminate labor and inventory waste
in the production process
Kanban uses a "pull production" model to reduce waste, which adjusts the production of materials based on consumer demand and supply.
People think of Kanban as a "lean production" technology, or a technology to avoid waste of labor and inventory. One of the ways that Kanban avoids waste is to use the "pull production" model, which regulates the production of goods according to consumers’ supply and demand.
Rely on Kanban standardization production goals, reduce overhead, improve efficiency, reduce obsolete inventory, improve flow, and prevent overproduction
After using the Kanban system, goods are produced according to the (demand) quantity required by the market, rather than through conventional methods (forecasting and estimating the quantity that may be required).
The earliest manufacturer to use Kanban was Toyota, but the inspiration for creating a Kanban system at Toyota came from observing how customers interact with supermarket products. The concept is simple. Customers only buy the goods they need from the supermarket, and the supermarket must always provide customers with available goods. The idea of completely avoiding waste (or just-in-time production) means that we only produce the required quantity of goods when we need it. In the application of Kanban in the manufacturing industry, it is essential to manage inventory levels to prevent waste. After mastering all the basic concepts related to Kanban, it is time to put everything into practice and see that the Kanban system is practical in practice.
When the Kanban system involves materials, the Kanban can be a card or a trash can. In this article, we only focus on cards. To briefly explain, using a paper slot instead of a card simply means that an empty paper slot is used as a signal to be replaced by a full paper slot, and an empty paper slot is sent for replenishment. When using a card, the card is attached to a batch of materials and only moves between processes.