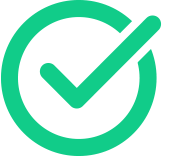
Kanban makes use of the principle that humans are visual animals, allowing teams to quickly learn corporate management, enabling companies to leapfrog and improve their management capabilities.
Kanban can provide you the following benefits:
Zero learning curve: Kanban allows users to use simple pictures and words to represent their contents and Kanban board columns to represent workflows and work-in-progress. Since learning it is a zero learning curve, a variety of users in your organization can learn this in no time.
Extreme versatility: The desire for operational efficiency is prompted by a need for adaptability. Kanban’s versatility enables all your employees to shift seamlessly between divisions, programs or projects, which helps your overall operation.
Increased visibility: Kanban board serves as the fundamental building block of this strategy. Its objective is to demonstrate the steps required to bring a concept to reality.
Efficiency: It is not unusual to use additional resources to resolve the issue more efficiently. Kanban takes a unique method, assisting you in increasing productivity while maximizing the use of existing resources.
Improved productivity: Higher efficiency inevitably results in additional benefits of productivity improvements. Kanban increases your performance by focusing your attention from starting to finishing tasks.
Workload reduction: Kanban uses Work In Progress (WIP) restrictions. When a WIP limitation is enforced, no new activities can be added to the current job until all current operations are completed, which helps everyone in remaining focused on the most critical work.
Collaboration: Using Kanban, everyone is aware of how other parties are performing, which increases productivity. Additionally, it motivates team members to collaborate and look for ways to improve.
Increased accessibility to information: Using Kanban is an efficient way to acquire organizational knowledge.
Kanban board collects and processes data from numerous staff members. This is advantageous for personnel who may lack a working knowledge of a more complicated approach.
By utilizing the above benefits of Kanban, you can develop a sustained competitive advantage.
Kanban architecture was designed to help users to visualize activities and responsibilities and manage schedules and progress of projects. An
Kanban project starts with a few columns (e.g., Requested”, “In Progress” and “Done”) defined in its type. When a Kanban card is being added, it will be insert in the column according to its status. When constructed, managed and functioning properly,
Kanban serves as a real-time information repository, highlighting bottlenecks within the system and anything else which might get in the way of smooth working practices.
Visualize the Workflow
The first and most important thing for you is to understand what it takes to get an item from request to a deliverable product. Only after understanding how the flow of work currently functions can you aspire to improve it by making the necessary adjustments.
To visualize your process with a Kanban system, you will need a board with cards and columns. Each column on the board represents a step in your workflow. Each Kanban card represents a work item.
When you start working on item X, you pull it from the “To Do” column and when it is completed, you move it to “Done”. This way you can easily track progress and spot bottlenecks.
Limit Work in Progress
Switching a team’s focus halfway through will generally harm the process, and multi-tasking is a sure route to generating waste and inefficiency; a primary function of Kanban is to ensure a manageable number of active items in progress at any one time. If there are no work-in-progress limits, you are not doing Kanban.
Limiting WIP means that a pull system is implemented on parts or all of the workflow. Setting maximum items per stage ensures that a card is only “pulled” into the next step when there is available capacity. Such constraints will quickly illuminate problem areas in your flow so you can identify and resolve them.
Manage Flow
The whole idea of implementing a Kanban system is to create a smooth healthy flow. By flow, we mean the movement of work items through the production process. We are interested in the speed and the smoothness of movement.
So, managing the flow is about managing the work but not the people. So instead of micro-managing people and trying to keep them busy all the time, we should focus on managing the work processes and understanding how to get that work through the system faster.
Ideally, we want fast and smooth flow. This would mean that our system is creating value quickly. This way we can minimize the average cycle time for production and avoid the cost of delay but in a predictable fashion.
Make Process Policies Explicit
You can’t improve something you don’t understand. This is why the process should be clearly defined, published and socialized. People would not associate and participate in something they do not believe would be useful.
When everyone is familiar with the common goal, they would be able to work and make decisions regarding a change that will move you in a positive direction.
Feedback Loops
In order for the positive change to happen, succeed and continue, one more thing needs to be done. The Lean philosophy supports the assumption that regular meetings are necessary for knowledge transfer (feedback loops).
Such are the daily stand up meetings for team synchronization. They are held in front of the Kanban board and every member tells the others what he or she did the previous day and what will be doing today.
There are also the service delivery review, the operations review, and the risk review meeting. The frequency depends on many factors, but the idea is that they are regular, at a strictly fixed hour, straight to the point and never unnecessarily long.
The ideal average length of a stand up should be between 10-15 minutes, and others may reach up to an hour depending on the team size and topics.
Improve Collaboratively
The way to achieve continuous improvement and sustainable change within an organization is through shared vision of a better future and collective understanding of the issues that need to be overcome.
Teams that have a shared understanding of theories about work, workflow, process, and risk are more likely to build a shared comprehension of a problem and suggest steps towards improvement, which can be agreed by consensus.