Special News
Which supplier management system is the best?
2024-08-08
From the current environment, supplier information management is the general trend. The supplier management system came into being under such a trend. Compared with traditional supplier management, the supplier management system emphasizes more on collaboration and win-win. I believe that in todays turbulent market, the strong connection and common destiny between enterprises are important weapons for enterprises to consolidate their foundations and expand their businesses.
What factors should a qualified supplier management system have?
Reduce procurement costs, efficiently screen high-quality suppliers, control product quality and delivery time, and establish a good supplier management system. The most important thing is to comply with the logic of supplier management and the operation is suitable for each employee.
What are the good supplier management systems?
1. 8Manage SRM
8Manage SRM procurement and supplier management software can help enterprises quickly connect with external suppliers and break down the barriers to procurement and supply collaboration. Internally, it helps enterprises build a procurement demand management center; externally, enterprises can conduct online business collaboration with suppliers across platforms and organizations. Through functional modules such as supplier life cycle management, strategic sourcing, procurement collaboration, and financial reconciliation, it helps enterprises achieve efficient and standardized procurement management.
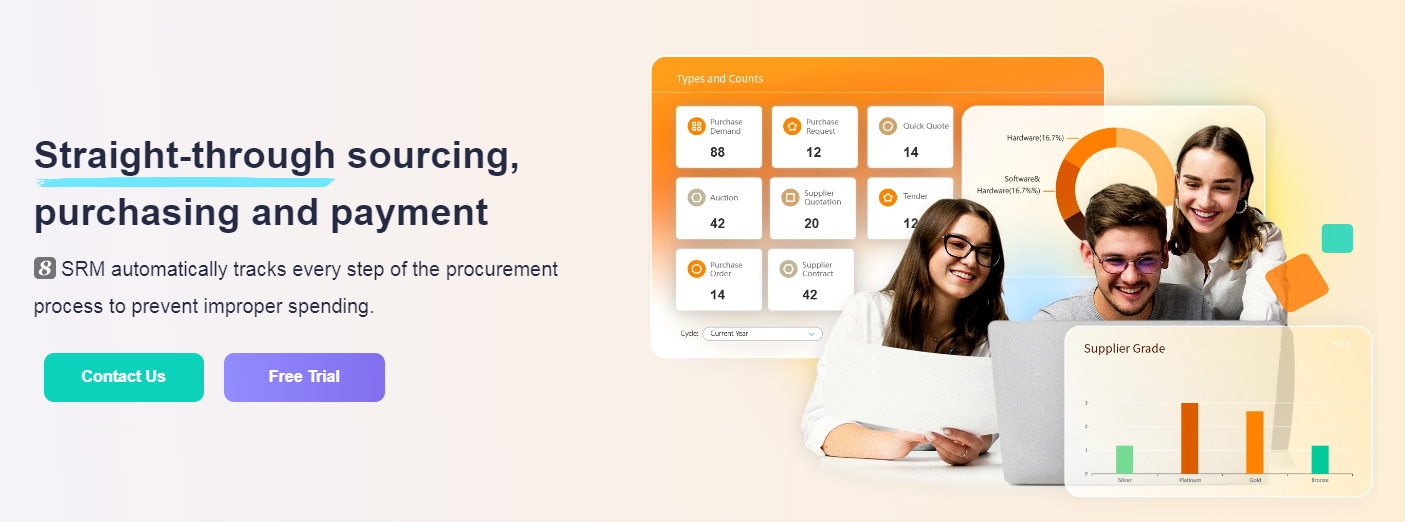
Highlights
Connect suppliers across platforms
● Supplier connection: invite suppliers through batch import or link, and collaborate based on different platforms such as DingTalk and WeChat;
● Permission setting: after setting permissions, suppliers can fill in data, view reports within permissions, and participate in the approval process;
● Information transparency: real-time synchronization of procurement needs, order contracts, shipments, reconciliation data, etc. of both parties.
Supplier life cycle management
● Standardized management process: access → assessment → rating → improvement and optimization;
● Supplier self-service portal is used to input supplier information, demand communication, etc.;
● Customized assessment model, automatic completion of periodic performance assessment.
End-to-end management of the entire procurement process
● Manage the entire procurement process from demand, sourcing to order execution, and build a closed business loop;
● Complete the review and settlement of each link online to achieve real-time transparency of procurement progress and data.
2. SAP Ariba
Founded in the last century, it started early and has a deep foundation. It is very complete in enterprise-side SRM functions. At present, it has covered multiple sub-solutions such as sourcing, contract management, procurement payment, procurement content, supplier management, etc., which can meet most of the needs, and the user interface looks relatively clear. However, there are only agents in China, and there may be some lags in after-sales and implementation.
Highlights
Procurement and contracts:
● Collect and classify all purchased items
● View total expenditures and determine sources of savings
● Standardize the entire workflow from procurement to contract
Supplier management:
● Prioritize spending on key suppliers
● Integrate supplier management functions with procurement
● Unify supplier records for management
● One-stop management of performance, life cycle, performance and risk
Procurement management:
● Handle direct, indirect and service expenditures
● Improve procurement through guided procurement
● Centralize data, analyze and gain insights
3. Oracle Procurement Cloud
Oracle Procurement Cloud is an SRM tool that integrates procurement and supply chain management. It provides functions such as supplier qualification, procurement, contract management, and supplier performance evaluation to help you proactively develop strategies to increase revenue and reduce costs, and monitor execution to ensure that goals are achieved.
Highlights
Supply Chain Planning: Plan supply, demand, manufacturing, manage sales and operations, and order fulfillment across the entire supply chain, allowing different teams to collaborate smoothly, minimize disruptions, and save costs.
Inventory Management: Control inventory flows in your location and global supply chain with built-in material management, cost management, and financial and supply chain coordination functions.
Procurement: Streamline the workflow from purchase to payment through an intuitive analysis and collaboration interface. It simplifies supplier management, including selecting suppliers, implementing compliant spending, and improving profitability.
4. Jaggaer
Jaggaer is a comprehensive procurement software that provides end-to-end SRM solutions covering supplier management, procurement, purchasing, and spending analysis. Its platform is designed to optimize supplier relationships, improve collaboration, and increase procurement efficiency.
Regarding SRM, Jaggaer provides supplier relationship insights through a flexible and intelligent supplier management solution.
Highlights
● AI Supplier Management
● E-Procurement and Sourcing Optimization
● Contract Management
● Purchase Order Management
● Compliance and Risk Management
● Business Intelligence and Reporting
The Jaggaer platform enables effective and efficient collection of supplier information and data, and also completes the initial steps of approving or reviewing suppliers to join the network. This helps to establish efficient and easy-to-manage supplier relationships.
Supplier Management System Process
The supplier management system process usually includes the following key steps:
Supplier identification and selection: The company first determines the required products or services and identifies potential suppliers.
1.Qualification review: Conduct qualification review of suppliers, including financial status, production capacity, quality control system, etc.
2.Evaluation and selection: Based on the evaluation results, select the most suitable supplier for cooperation.
3.Contract negotiation: Negotiate with suppliers on terms such as price, delivery time, quality standards, etc., and sign a contract.
4.Order management: Place orders, track order status, and ensure on-time delivery.
5.Supply chain coordination: Coordinate various links in the supply chain to ensure smooth logistics and information flow.
6.Performance evaluation: Regularly evaluate the performance of suppliers, including delivery time, product quality, service level, etc.
7.Risk management: Identify and manage risks that may arise in the process of cooperation with suppliers.
8.Relationship maintenance: Establish long-term cooperative relationships and continuously optimize cooperation through communication and feedback mechanisms.
9.Continuous improvement: Continuously optimize supplier management strategies based on market changes and corporate needs.
10.This process helps ensure that suppliers can continue to provide high-quality products and services while reducing costs and risks.
The above is a general description of the supplier management system process. Users can adjust and optimize it based on this to meet their own special needs. I hope this article will help you understand which supplier management system is better.
Most popular
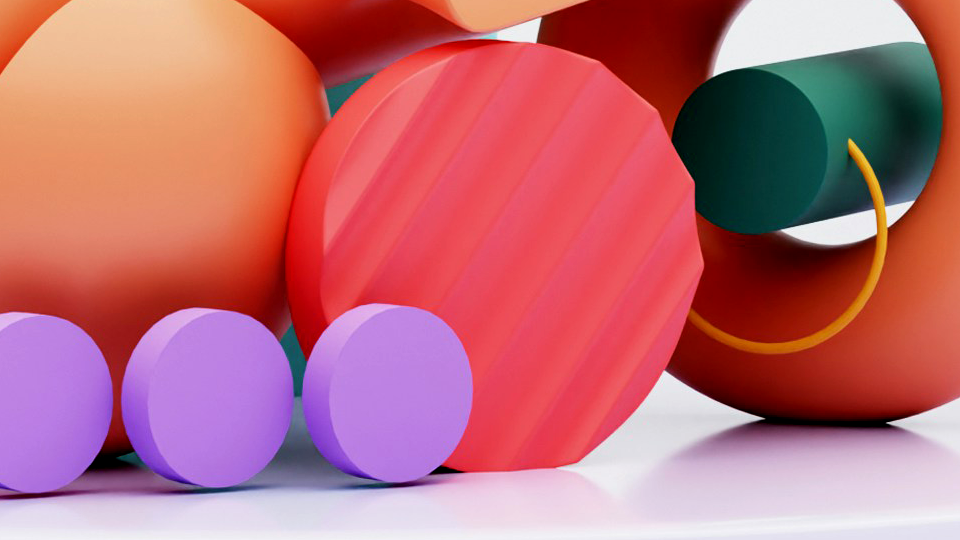
How IPD drives product R&D toward commercial success
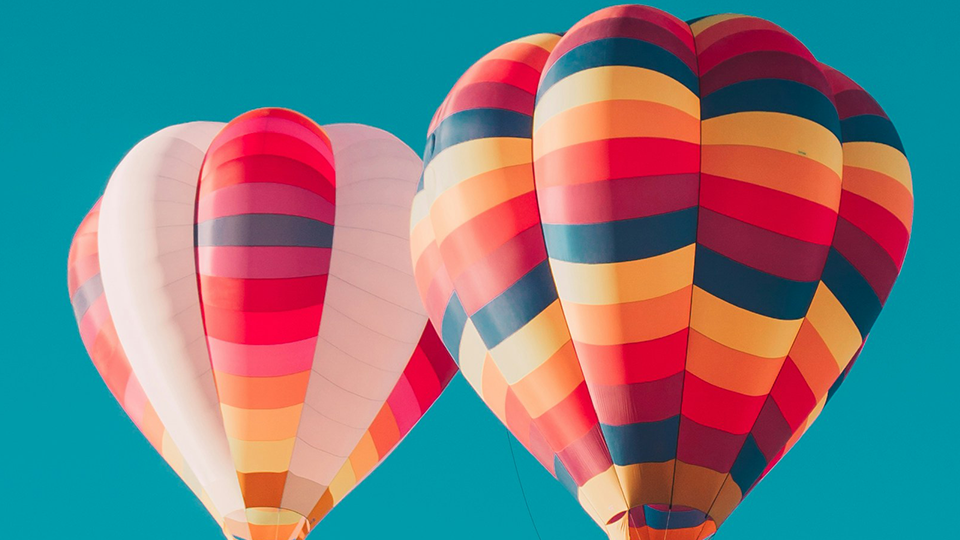
Top procurement management systems to elevate your business in 2025
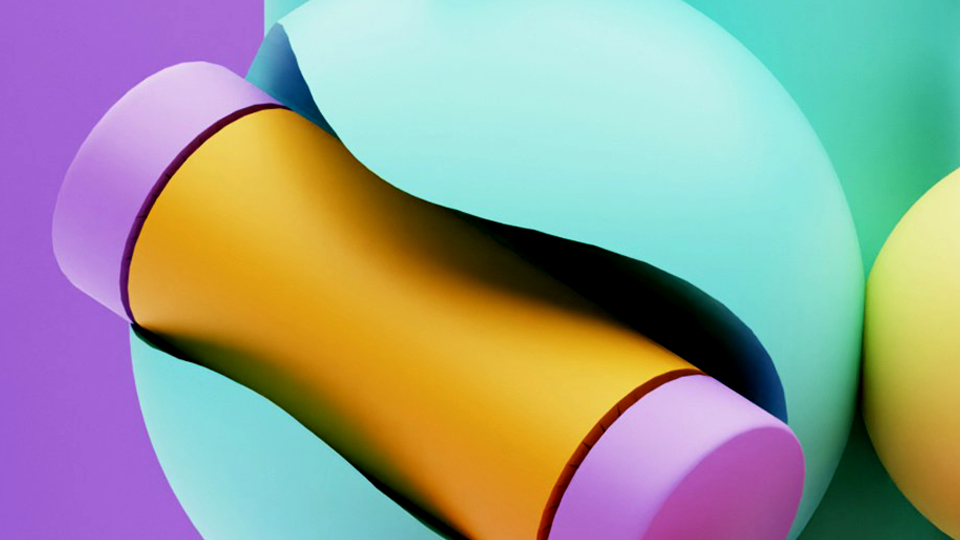
Are your project managers ready for AI?
Related articles
Real estate procurement management system selection guide
2025-02-13
2025 Guide to supplier management systems for manufacturers
2025-01-24
Hotel procurement and cost control: Your key to higher revenue
2025-01-16
Top procurement management systems to elevate your business in 2025
2025-01-10
Key nodes in automotive supply chain: Logistics, procurement, cost
2025-01-08
Previous Article >
8Manage PM: Your Solution for IT Project Efficiency
8Manage PM: Your Solution for IT Project Efficiency
Next Article >
Procurement management software: why is it so useful?
Procurement management software: why is it so useful?