What is Manufacturing Project Management?
2024-11-04
Manufacturing project management refers to the process of managing and coordinating various project activities in the manufacturing industry to achieve the effective production of products. Such projects usually involve complex resource allocation, process optimization, cost control, and quality management, aiming to ensure that products are completed on time and with high quality and meet market demands. Manufacturing projects are very common in modern industry and are an important means for manufacturing enterprises to achieve large-scale production, control costs, and improve quality. This article will discuss in detail from multiple aspects such as the definition, characteristics, process, advantages, and challenges of manufacturing projects to help you gain a deep understanding of what manufacturing project management is.
1. What is Manufacturing Project Management?
Manufacturing project management refers to the whole-process management of project planning, execution, monitoring, and closing in the manufacturing industry, ensuring that manufacturing projects are completed on time, within budget, and in accordance with quality standards. Its core is to effectively control each stage of the project (from product design to production and then to delivery) by coordinating resources such as manpower, equipment, and materials. Manufacturing project management not only focuses on project progress but also pays attention to risk management, quality control, resource allocation, and cost management to improve production efficiency, reduce operational risks, and achieve project goals.
2. The Main Characteristics of Manufacturing Projects
Manufacturing projects have some notable characteristics that distinguish them from other types of projects in project management:
- Complex process flows: Manufacturing projects usually involve multiple complex production processes, including the procurement of raw materials, production processing, assembly testing, etc. These processes are interrelated, and any delay or error in any link will affect the overall production efficiency. Therefore, manufacturing projects require detailed process planning and precise task allocation.
- Multi-party collaboration requirements: In manufacturing projects, the collaboration of multiple departments or teams is often required, such as design, procurement, quality control, production workshops, and sales departments. To ensure the smooth completion of the project, the collaborative operation and information sharing among departments are crucial.
- Strict quality standards: Manufacturing projects are required to strictly follow the quality standards set by the industry and the company to ensure that the final product meets the needs and safety regulations of customers. Multiple quality inspection points are usually set in manufacturing projects to promptly detect and correct problems that occur during the production process to ensure the quality of the product.
- High cost sensitivity: Since manufacturing projects involve the use of a large amount of raw materials, manpower, and equipment, cost control is crucial. Any waste of resources will directly affect the overall profitability of the project, so strict budget management and cost control measures are required.
3. The Management Process of Manufacturing Projects
The management process of manufacturing projects can be divided into the following stages, and each stage has its specific tasks and goals:
3.1 Requirement Analysis
The first step in a manufacturing project is to conduct a detailed requirement analysis to clarify the final goal, technical requirements, and market positioning of the project. During the requirement analysis stage, the project team needs to communicate with the customer or the market department to understand the design requirements, functional requirements, and quantity requirements of the product. This stage helps the project team determine the required resources, budget, and time arrangement, providing a clear guide for the subsequent production process.
3.2 Resource Allocation
After clarifying the project requirements, the project team needs to allocate resources. Resources include manpower, equipment, materials, and funds, etc. The project team needs to reasonably allocate and manage these resources to ensure that each production link can proceed smoothly. Resource allocation should not only consider the current needs but also have a flexible adjustment plan to deal with possible unexpected situations.
3.3 Process Planning
The process planning of a manufacturing project is one of the core contents of project management. Process planning includes formulating a detailed production plan, determining the sequence, completion time, and quality requirements of each production link. Scientific process planning can improve production efficiency, reduce resource waste, and minimize the risk of delay. This stage will also optimize the production process and maximize the utilization of resources to ensure the smooth progress of production.
3.4 Production Execution
After the completion of resource allocation and process planning, the project enters the production execution stage. At this stage, the production team operates according to the established plan and completes the manufacturing of the product according to the design specifications and quality requirements. Any problems or anomalies during the production execution process will be promptly recorded and reported so that the project manager and the management team can make rapid adjustments.
3.5 Quality Control
The quality control of a manufacturing project runs through the entire production process, ensuring that the product meets the design and quality standards through multi-level inspections and tests. Quality control mainly includes the inspection of raw materials, the monitoring of the production process, and the testing of the final product. A strict quality control system can effectively reduce the rate of nonconforming products and enhance the market competitiveness of the product.
3.6 Project Evaluation and Delivery
When the product is manufactured and passes the quality inspection, the project enters the evaluation and delivery stage. The project team will review the entire manufacturing process, evaluate the success and deficiencies of the project, and record relevant data for future reference. Before delivery, the project team will check the product quality again to ensure that the delivered product meets the customers needs and the companys standards.
4. The Challenges Faced by Manufacturing Project Management
Although manufacturing project management has many advantages, it also faces many challenges in actual operation:
- Supply chain risks: Manufacturing projects highly depend on the supply chain, and any interruption in any link of the supply chain may lead to production delays. Especially in todays globalization, the fluctuation risks of the supply chain are greater.
- Technical and process complexity: Manufacturing projects often involve complex production techniques and processes, and any process problem will lead to a decrease in efficiency or quality problems. Project managers need to ensure that the project team is familiar with relevant techniques and can effectively manage each production process.
- Cost pressure: The cost pressure of manufacturing projects is extremely high, especially when the price of raw materials fluctuates greatly. Enterprises need to maintain profit margins through more strict budget control.
- Resource allocation and coordination: Manufacturing projects often involve a large amount of resource requirements, such as manpower, equipment, raw materials, etc. How to effectively allocate resources among different projects while avoiding resource waste is a complex task.
- Quality control (https://www.8manage.com/pm/quality.html): In a high-standard and strict-requirement manufacturing environment, product quality is crucial. Project management needs to conduct strict quality monitoring at each production stage to ensure that the product meets the specification standards. Lack of effective quality control will lead to rework and increased costs.
- Progress control: The time of manufacturing projects is usually relatively tight, and the schedule is affected by multiple variables. Project managers need to monitor the project progress in real time, adjust the task priorities, to avoid the impact of delays on the delivery time.
- Risk management: There are many potential risks in manufacturing projects, such as changes in market demand, technical failures, safety issues, etc. Project managers need to identify and evaluate risks in advance and formulate countermeasures to minimize the impact on the project.
- Communication and collaboration difficulties: Manufacturing projects often involve the close cooperation of multiple departments, and communication barriers between different departments may affect the smooth progress of the project, requiring a perfect communication mechanism.
8Manage PM is a project management software based on manufacturing projects. Whether an enterprises business is designed according to orders, produced according to orders, configured according to orders, or assembled according to orders, 8Manage PM allows the management of customer relationships, requirements, contracts, bill of materials (BOM), manufacturing activities, human resources, deliverables and delivery, quality and service level agreements, payment milestones and settlement as projects for each customer order. Learn more: https://www.8manage.com/ppm_index.html
Related Questions FAQs
1. What is the difference between manufacturing projects and other types of projects?
The key difference between manufacturing projects and other projects is that it revolves around the production process of actual products, while other projects such as software development or construction projects may focus more on technical development or construction management. Manufacturing projects usually have complex production processes and strict quality standards, requiring project managers to have a comprehensive understanding of the production process. In addition, manufacturing projects are more sensitive to cost and time and often involve multi-departmental collaboration to ensure the efficient use of resources and the timely delivery of products.
2. How to effectively control the cost of manufacturing projects?
Methods for controlling the cost of manufacturing projects include: formulating a detailed budget plan in the early stage of the project, controlling the expense of each production link; conducting precise resource allocation to avoid unnecessary resource waste; strictly controlling in the procurement and production processes to ensure high-performance-price-ratio materials and equipment; and monitoring each link in the production process to promptly detect and solve possible cost overrun problems. In addition, regularly analyzing the cost structure of the project and timely optimizing resource allocation and process are also crucial.
3. How to deal with supply chain interruptions in manufacturing projects?
Supply chain interruption is a common risk in manufacturing projects. Methods for dealing with supply chain interruptions include: establishing an alternative supplier network so that it can be quickly switched when the original supply chain is interrupted; conducting moderate inventory storage of key raw materials to deal with short-term supply chain fluctuations; using a supply chain management system to monitor the supply chain in real time to discover potential risks; in addition, it is possible to constrain the supply stability of suppliers through contracts to reduce the impact of supply chain interruptions on the project.
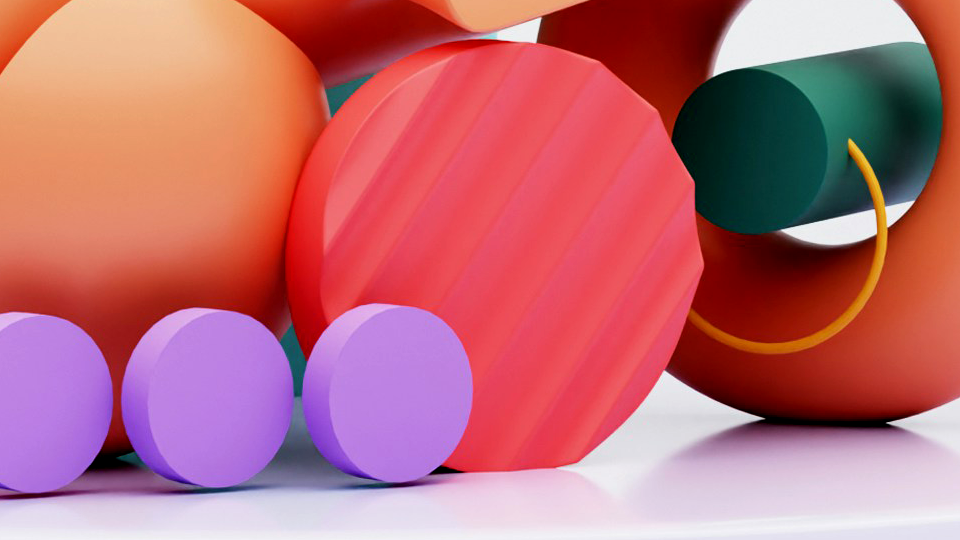
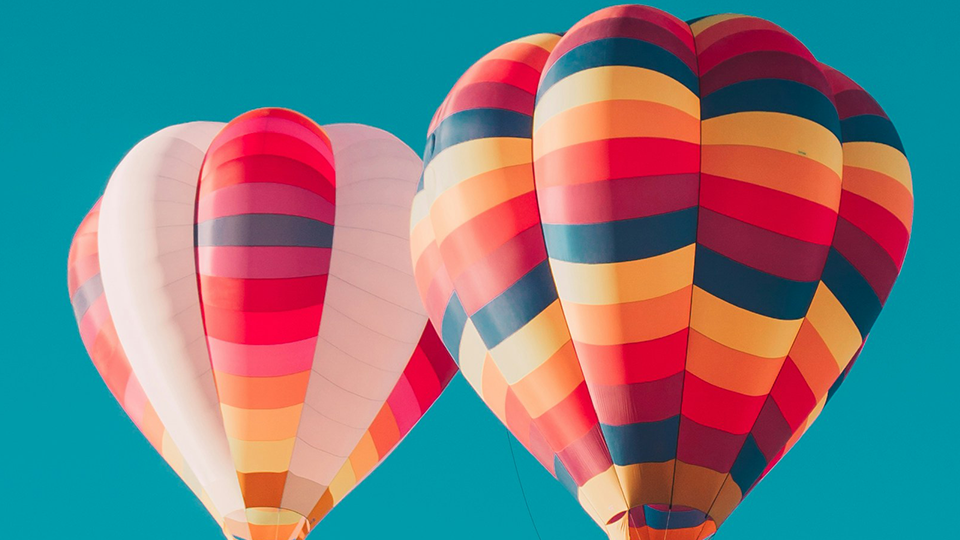
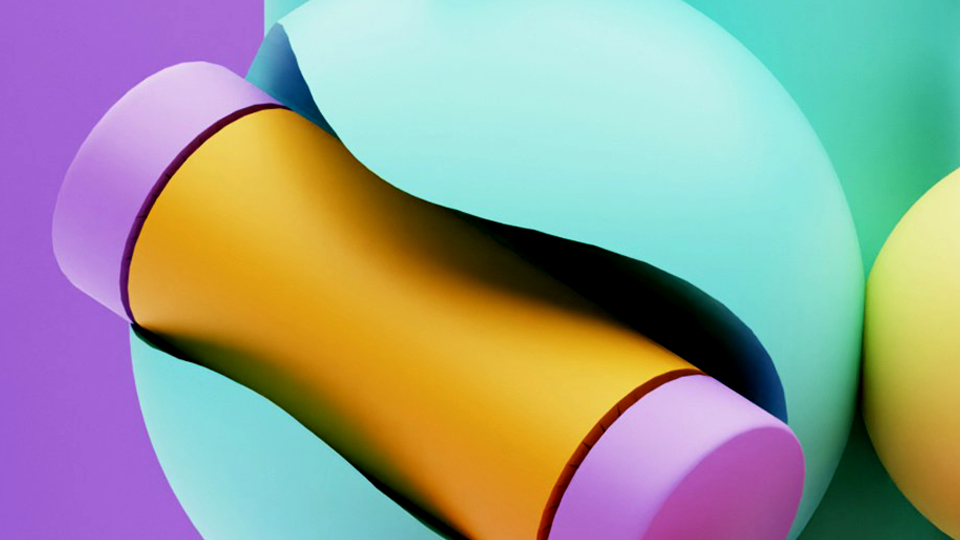
What is Digital Project Management?
What is e-Auction in Procurement?